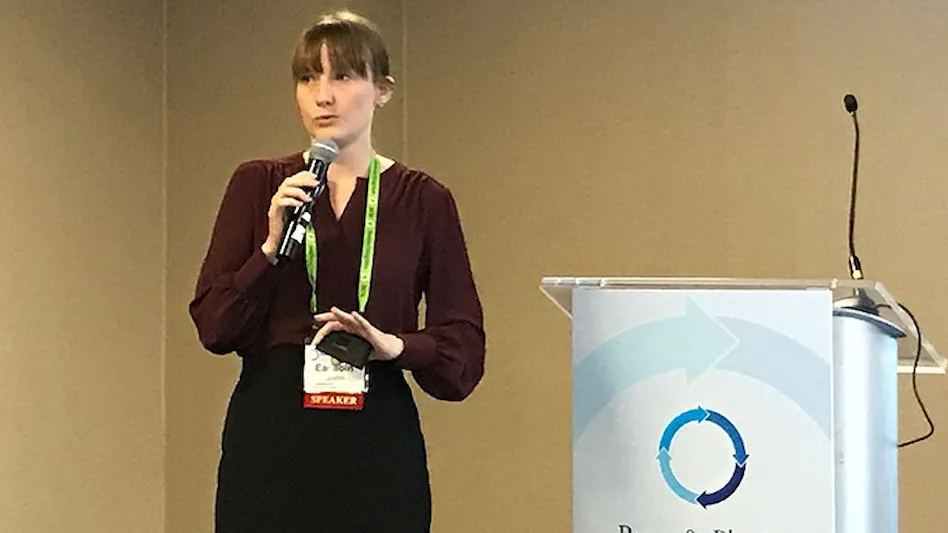
A report by Closed Loop Partners, New York, that is to be released in November will examine polypropylene (PP) recovery at material recovery facilities (MRFs). The group’s Director of Special Projects Jon Powell gave attendees of the 2019 Paper & Plastics Recycling Conference workshop Polypropylene Roundtable: Processing- and Market-Based Perspectives on Keeping PP in the Recycling Stream a preview of the study.
Powell said the project grew out of Keurig Dr Pepper’s interest in seeing whether its PP coffee pods could be recovered at MRFs. Radio-frequency identification (RFID) tags were affixed to the pods before they traveled through MRFs, revealing that 90 percent of these pods made it to the container line for further sorting, Powell said.
However, concerns related to China’s National Sword have led some MRFs to discontinue preparing bales of Nos. 3-7 plastics, which could potentially have a negative effect on PP recovery.
The Closed Loop study involved evaluating the supply chain to see where bottlenecks were arising, he said. Powell noted that many North American plastics reprocessors have excess capacity to handle PP.
KW Plastics Director of Market Development Stephanie Baker said the Troy, Alabama-based company is operating at 60 percent to 70 percent below its rated capacity.
However, issues at the MRF are affecting the supply chain.
Robotic sorters and optical sorters can be installed at MRFs to address this bottleneck, Powell said. In facilities with less inbound material, he said robots are more appropriate, while optical sorters are more appropriate in MRFs that process large tonnages. “If we are going to meaningfully recover PP at some sort of scale, we need some sort of mechanical intervention,” Powell added.
He offered three scenarios for analyzing the return on investment (ROI) for positively sorting PP at a MRF:
- MRFs with 18,000 tons of inbound material will see an ROI of that ranges from 2.8 to 4.5 years.
- Those handling 40,000 tons of inbound material will see an ROI in the range of 3 to 4.9 years.
- MRFs processing 80,000 tons of inbound material will see an ROI of 3.7 years.
Powell said robotics can be programmed to sort by a hierarchy of need, therefore the ranges above depend on the robot’s availability to pick polyethylene terephthalate (PET) once the PP sort has been satisfied.
PP has a value and market pull, he added. “The odds are that aggressive commitments to use PCR (postconsumer recycled resin) will pull material into the market.” However, Powell advised that MRF operators look at their incoming material streams “with vigor” to confirm their PP contents prior to investing in recovery.
Ron Chislow, president and chief operating officer of Buckeye Polymers, Lodi, Ohio, said his company reprocesses and compounds 24 million pounds of postconsumer plastics, including PP, annually. Much of the company’s recycled PP goes into automotive applications, which he said has had “a lot of fits and starts related to recycled feedstock.”
For years, recycled PP has been sold as cheaper alternative to virgin until recently, said Eadaoin Quinn, director of business development and procurement for EFS Plastics Inc., headquartered in Canada. However, the material has not been marketed as recycled content necessarily.
She added that she has felt a real shift in terms of PP demand in the last two months as brands trial her company’s material to label as recycled-content material. But, she added, the trials have not yet translated to purchase orders.
Baker said she has been encouraged by Walmart’s commitment to use 20 percent PCR in its private label product packaging by 2025, adding that the company is encouraging its other suppliers to follow suit.
Alan Handley, CEO of Chicago-area-based Lakeshore Recycling Systems offered the perspective of a MRF operator. The company processes largely commercial material at its MRF, with PP representing 0.14 percent of the incoming material stream, he said.
“We are constantly evaluating ways to remove labor from recycling operation,” Handley said. “We have to pull cost out to be effective,” he added, which is why the company installed robotic sorting recently.
Robotics is not a “one-size-fits-all situation,” Handley said, explaining that the systems need to be sized and specified to the product a MRF is picking.
EFS Plastics is sorting at the flake level to recover and reprocess Nos. 2, 4 and 5 plastics primarily from the mixed bales it purchases, though it also can recover some of the No. 7s. The plastics the company cannot process are going to waste-to-energy applications, Quinn says.
MRFs have a “big misconception that markets don’t exist” for Nos. 3-7 bales, Baker said.
Prior to China’s ban on postconsumer plastic scrap imports, Quinn said MRFs were removing the Nos. 1-2 and producing mixed plastics bales that they shipped to China. She said that in some cases that mixed plastic bale is really residue coming and needs to be cleaned up before going to market. However, if those bales are mostly plastics, Quinn explained, “that is a stream that we are set up for.” She added, “We can make a true PP with more than 80 percent yield.”
Cost is the main component that will drive everything, Chislow said, adding that Buckeye doesn’t want to do anything that will add another layer of cost to the process. He said MRFs must understand what can’t be in their mixed plastics bales.
Handley said the future in the Midwest as he sees it is tying MRF operators and processors closer together, so material does not have to be transported 600 or 800 miles away. “We have to have the reprocessors closer to us,” he said. “We have to solve that problem and tie us all together with the consumer goods people.” Handley added that tightening up the supply chains was a goal everyone should be working on.
The 2019 Paper & Plastics Recycling Conference was Oct. 23-25 in Chicago. The 2020 event is planned for Oct. 21-23.